Screen printing on membrane panels can achieve a variety of functions and effects, enhancing the quality of product appearance, functional performance, and market competitiveness. It can also meet the design and demand requirements of different products. Through screen printing technology, various logos, patterns, text, or images can be printed on membrane panels for product identification, brand display, or functional indication. These printed designs can assist users in operating the product or understanding product information more easily. Fine screen printing can produce high-resolution, colorful, and diverse patterns to enhance the appearance of membrane panels. Additionally, by using special functional inks, products can be made conductive, flame retardant, fluorescent, and possess other special features.
Membrane switches and membrane overlay can utilize a variety of screen printing process options in the manufacturing process. Screen printing technology offers numerous advantages in the production of membrane panels, including, but not limited to, the following
Single Monochrome Screen Printing: Monochrome screen printing is the most basic and commonly used screen printing process, where a single color pattern or text is printed on the surface of the film by a screen printing machine. This process is simple, low-cost, and suitable for printing some simple patterns and logos.
Multi-colour screen printing: Multi-color screen printing involves printing different colors of patterns or text sequentially on the film surface to achieve colorful and diverse effects through multiple screen printing overlays. This process demands high precision in printing and color matching, making it ideal for membrane switch manufacturing that necessitates rich colors and patterns.
Transparent Screen Printing: Transparent screen printing is a specialized printing process that utilizes transparent ink or transparent thermosetting ink to create transparent patterns. This technique is often employed in the design of membrane switches that require transparent patterns or backgrounds.
Metal Silk Screen Printing: Metal silk screen printing involves the application of metallic-colored patterns or text onto the surface of a film. Commonly used metallic colors include gold, silver, and copper. Metallic silk screen printing provides a glossy texture that enhances the high-grade appearance of the product.
Fluorescent Screen Printing: Fluorescent screen printing is the process of using fluorescent or luminescent inks to create designs that appear fluorescent when exposed to specific light. This technique is commonly employed for membrane switch designs that necessitate an indicator function or for providing visual guidance in low-light conditions.
Conductive Screen Printing: Conductive screen printing technology involves printing conductive ink on the surface of membrane panels to create circuit patterns or conductive contacts for electrical connections and signal transmission. This technology is commonly utilized in the production of touch screens, keyboards, and other membrane panels that require conductive features.
Pattern screen printing technology: Pattern screen printing technology is used to print various patterns, logos, or words on the surface of the film panel. This technique is employed to enhance the appearance of the product, display functional instructions, brand logos, and more. By utilizing pattern screen printing technology, product personalization and visual effects can be achieved.
Flame-retardant screen printing technology: Flame-retardant screen printing technology involves the printing of flame-retardant inks or fire-retardant coatings on the surface of thin-membrane panels to enhance the flame-retardant properties of the product and mitigate the risk of fire. This technology is frequently employed in the production of electronic products that have stringent safety standards.
Textured Screen Printing Technology: Textured screen printing technology involves printing a design with a textured feel on the surface of the film panel. This process enhances the tactile experience, aesthetics, and non-slip properties of the product. It is frequently utilized in the production of items like mobile phone cases and electronic device housings.
Membrane panels can be manufactured using a variety of screen printing techniques to achieve various product designs and functional requirements.
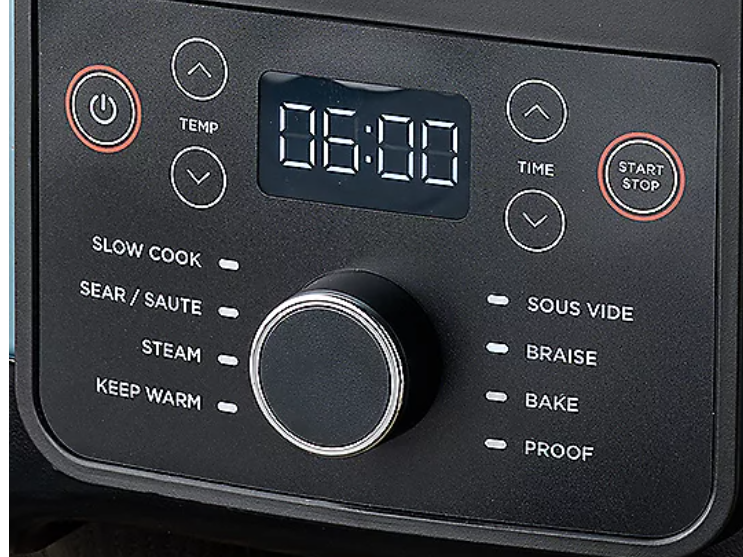
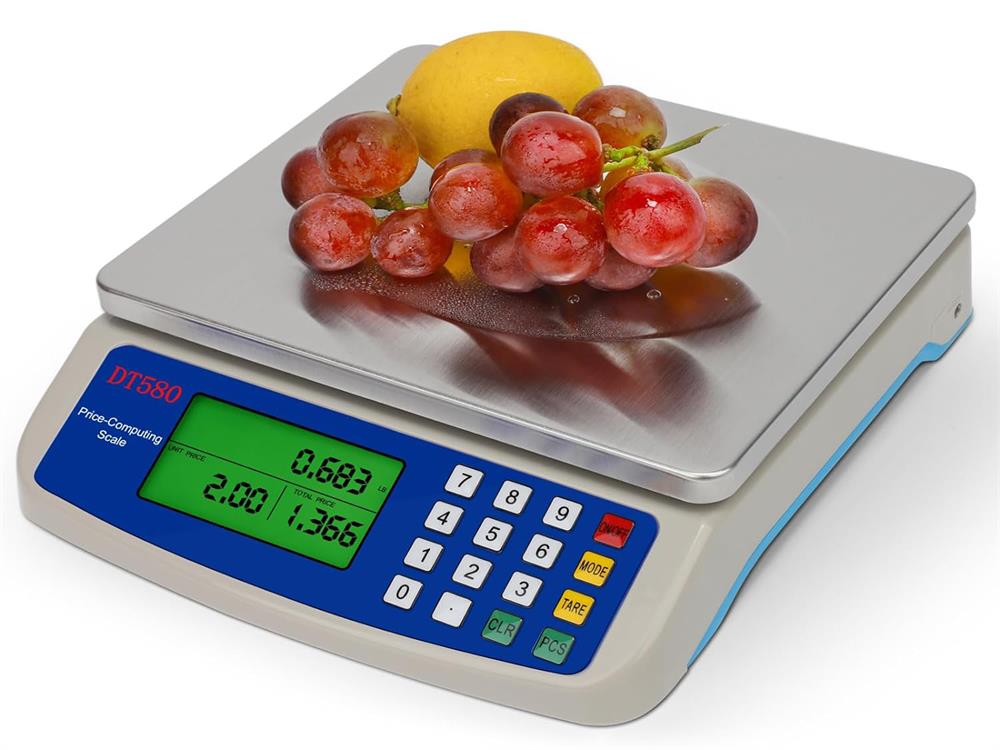
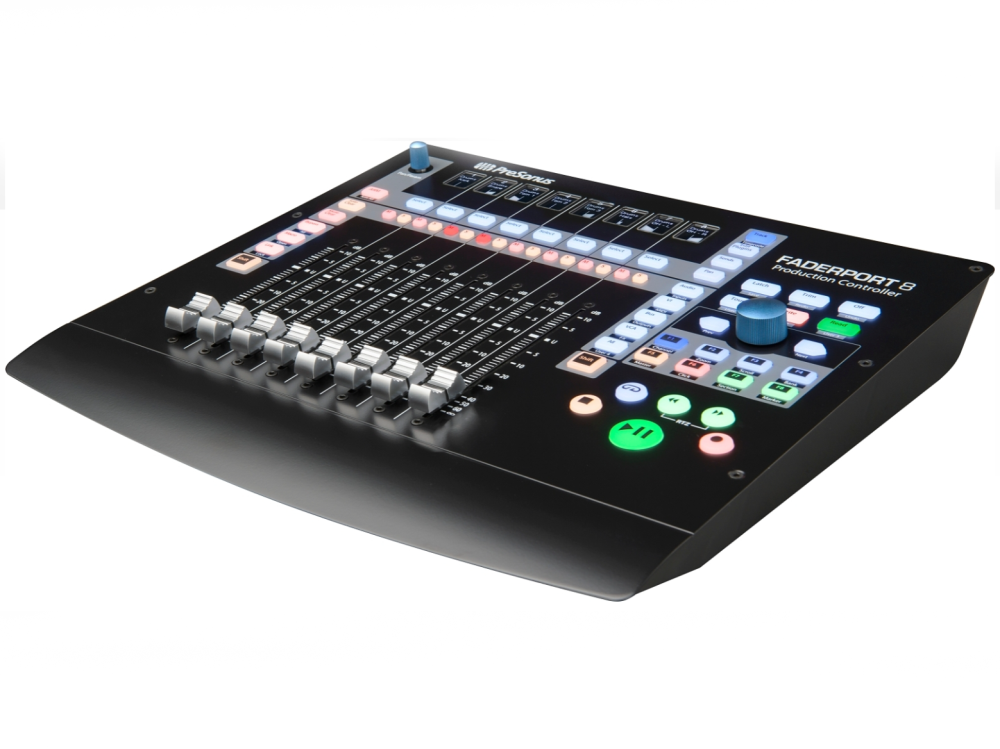
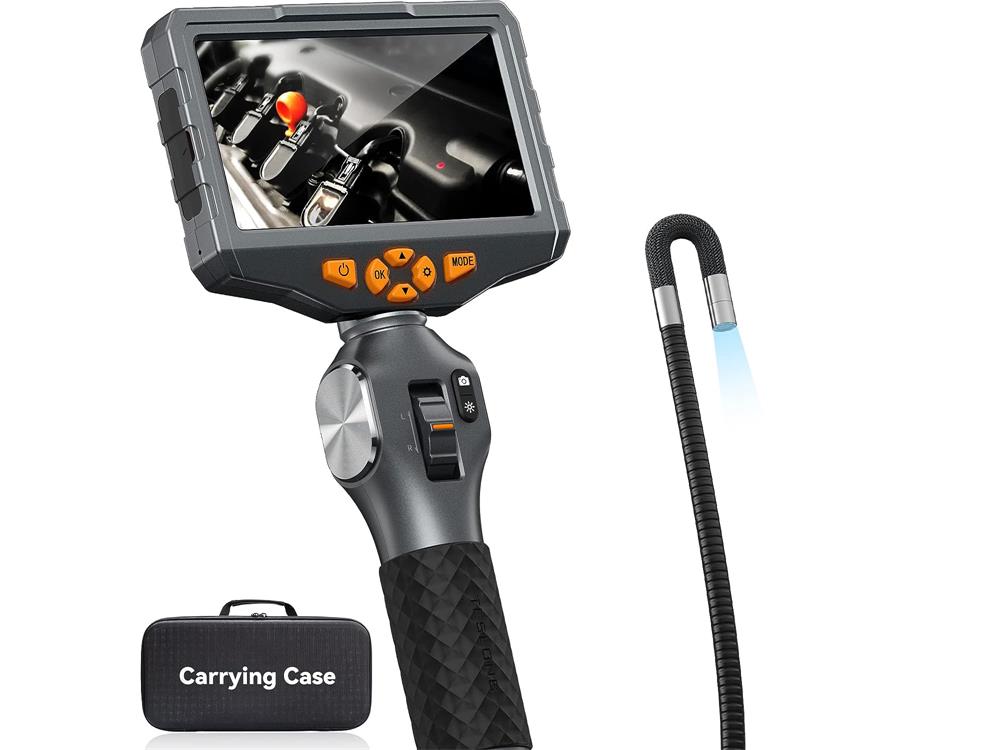