A rubber case is a protective cover made of silicone material that is frequently utilized to safeguard electronics, tools, or other items from external damage, abrasion, or vibration. Silicone is a flexible and pliable material with exceptional resistance to aging, high and low temperatures, chemicals, and electrical insulation. This makes silicone an ideal choice for use in protective sleeves that provide effective protection.
Silicone protective sleeves typically possess the following characteristics:
1. Anti-shock and anti-impact: Silicone possesses good softness and elasticity, enabling it to absorb external shocks and vibrations, thereby reducing damage to items.
2. Anti-slip and anti-fall: Silicone exhibits a certain level of viscosity, enhancing the grip on items and preventing them from slipping out of hands and sustaining damage.
3. Waterproof and dustproof: Silicone demonstrates excellent resistance to water and dust, effectively blocking their entry and safeguarding items from damage and contamination.
4. Anti-scratch: Silicone boasts high abrasion resistance, offering a certain level of protection against scratches and scuffs.
T he processing of the rubber protective cover mainly involves the following steps:
1. Raw material preparation: Prepare the required silicone material, typically liquid silicone, and other necessary auxiliary materials.
2. Mold design and fabrication: Design and fabricate the corresponding mold based on the shape and size of the product. The molds can be silicone injection molds or compression molds, among others.
3. Silica gel preparation: Mix liquid silica gel with a silica gel catalyst in the required ratio to promote the curing reaction of the silica gel.
4. Injection or pressing: Place the mixed silica gel into the pre-designed mold. For silicone injection, an injection machine can be used to inject the silicone into the mold. For press molding, pressure can be applied to insert the silicone into the mold.
5. Flattening and de-aerating: Flatten and de-aerate the silicone gel after injection or pressing to ensure even distribution within the mold and to remove air bubbles.
6. Curing and hardening: Silicone protectors must be cured and hardened under appropriate temperature and time conditions. This can be achieved through natural curing, oven curing, or accelerated curing.
7. Demolding and finishing: Once the silicone has fully cured and hardened, the protective sleeve is removed from the mold, and necessary finishing, trimming, and cleaning are performed.
8. Quality control and packaging: The silicone protective sleeve undergoes quality checks to ensure it meets standard requirements. Packaging is then carried out for product transportation and sale. These steps can be adjusted and optimized based on specific processing and product requirements.
It is important to note that the silicone processing process must adhere to appropriate safety regulations to ensure the safety of operators and products.
The design of silicone sleeves is typically customized to fit the shape and size of the item being protected, ensuring an ideal fit and effective protection. Silicone cases are extensively utilized in various applications, including mobile phones, tablets, controllers, tools, and more, offering additional protection and a convenient user experience.
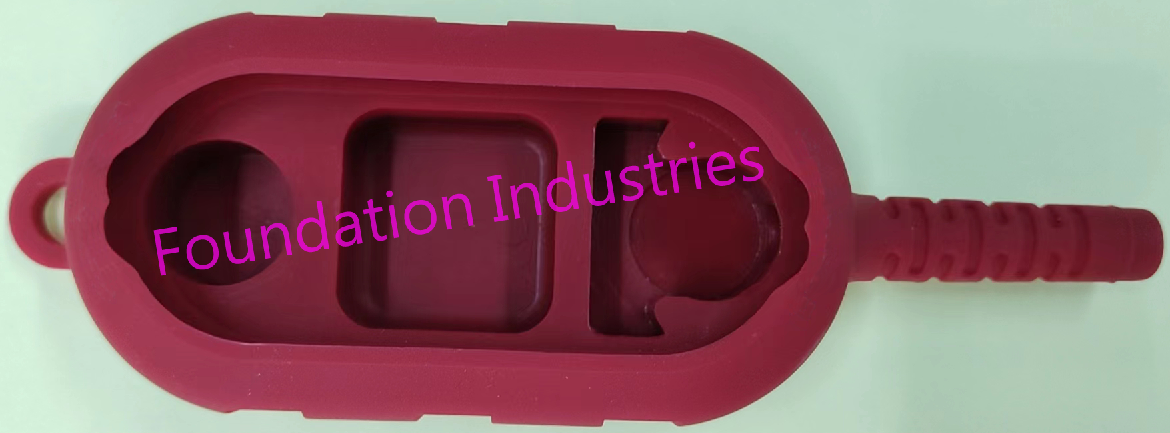
Post time: Nov-24-2023